Steel corrosion from chloride input
In the case of components with a high chloride load (e.g. components in the spray mist and splash water area of de-icing agent treated traffic areas), chloride ions dissolved in water are transported locally up to the reinforcement. Here, a localised corrosion, so-called pitting, takes place on the steel surface. Due to the small corrosion focus, this type of corrosion is not visible from the outside. However, the diameter of the reinforcing steel is greatly reduced and may even lead to failure of individual components.
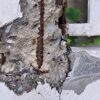
Steel corrosion due to carbonation
By the penetration of CO² into the concrete edge zone, the calcium hydroxide contained in the concrete is converted into calcium carbonate. Calcium carbonate is denser and harder than the concrete itself, but has a lower pH-value which no longer protects the steel from corrosion with a passive layer. If an electrolyte (usually water) touches the reinforcement, large areas of corrosion will occur. The first visible signs of this on the concrete surface are cracks, rust flags and flaking of the concrete cover.
Crack formation
Concrete components are reinforced in the area of occurring tensile forces by inserted reinforcement. When the tensile force of the concrete is exceeded, the reinforcing steel absorbs the tensile forces. Thus, evenly distributed cracks with small crack widths appear at each component subjected to tensile or bending stress. These cracks are part of the supporting structure and are not of further concern. However, unplanned cracks also occur in concrete structures, a distinction being made between cracks near the surface and separating cracks.
Cracks close to the surface usually have small crack widths and depths. This is usually caused by a rapid loss of water during the hardening phase (early shrinkage) and setting of the fresh concrete. To maintain durability, these cracks should be closed to prevent the penetration of corrosion-promoting substances.
Separation cracks become a concern from a larger crack width (usually > 0.4 mm). Causes for this are e.g. external forces, static reasons (overloading, support lowering, etc.), external temperature effects and the dissipation of the heat of hydration. To determine the cause of damage, lengthy investigations (crack monitoring) are necessary. If there are doubts about the load-bearing capacity, a structural engineer must be consulted.